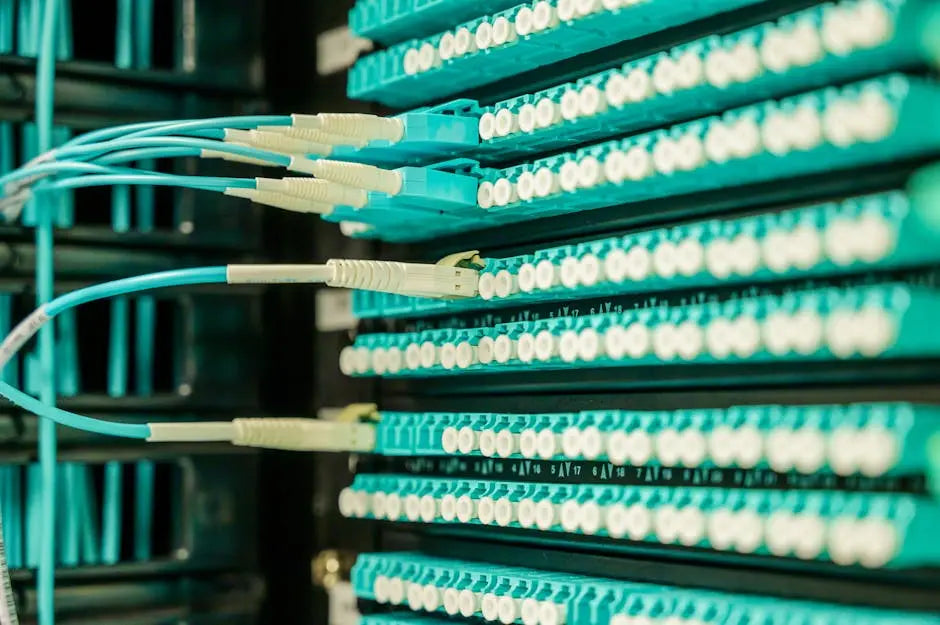
Choosing the Right Cable Clamps for Your Project
Share
Choosing the right cable clamps is essential for ensuring the safety and organization of your cables. Whether you’re working on a small DIY project or a large industrial installation, understanding the different types of cable clamps and their uses can make your task much easier. In this blog, we’ll explore the key considerations for selecting cable clamps that best suit your needs.
Understanding Different Types of Cable Clamps
Cable clamps come in various forms such as P-clamps, J-hooks, and saddle clamps. Each type serves a specific purpose and is best suited for certain applications. P-clamps, for example, are commonly used for securing cables to a flat surface due to their prevalent circular opening with a fastener on one end and a loop on the other. These are particularly popular in automotive and industrial sectors for maintaining cables in a controlled manner. J-hooks, on the other hand, are great for supporting horizontally run cables due to their open-sided design, allowing for quick installation. Lastly, saddle clamps are ideal for more permanent fixtures where stability and rigidity are essential. By knowing the specific uses and advantages of each type, you can decide which cable clamps work best for your project.
In addition to the traditional types, there are also specialized cable clamps designed for unique needs. For instance, adjustable cable clamps offer versatility and can be customized to accommodate various cable sizes, which is particularly useful in dynamic environments that require regular adjustments. Meanwhile, quick-release clamps are perfect for scenarios where cables need frequent access, as they provide a convenient mechanism for swift attachment and detachment. Understanding these types can be beneficial if your project involves ever-changing cable layouts. Familiarize yourself with these options so your project can benefit from enhanced flexibility and ease of modification.
To make an informed decision, consider factors such as load capacity, geographical location, and specific usage requirements. For projects involving sensitive cables or complex networks, investing in specialized variants like rubber-lined or foam-lined clamps can provide additional protection against abrasions and vibrations that might otherwise damage the connections. Exploring these types ensures you’re equipped to select a product that aligns with not just your immediate needs but also your longer-term requirements, reducing future maintenance and replacement costs.
Factors to Consider When Choosing Cable Clamps
When selecting cable clamps, consider factors such as the clamp material, cable diameter, and environmental conditions. The material of the clamp can range from plastics that offer affordability and ease of handling to metals that provide greater durability and load-bearing capacity. Depending on the project’s location, you might want to choose clamps that are UV resistant or suitable for high-temperature environments. Choosing the right material can prevent degradation over time and ensure your installation remains robust.
Another vital consideration is the cable diameter and how it relates to the clamp size. Measuring the diameter accurately is paramount; clamps that are too large or too small can lead to ineffective cable management or even cable damage. Furthermore, observe the clamp’s closure mechanism—are you opting for a fixed closure or an adjustable one? Fixed closures provide a solid grip but lack flexibility, whereas adjustable clamps cater to cables with varying diameters or expand to hold multiple cables tightly.
The environmental conditions where the clamps will be positioned also play a critical role. For instance, projects positioned outdoors or in damp environments might necessitate the use of clamps that are specially coated to resist rust and corrosion. Conversely, indoor setups located in dry, climate-controlled spaces might allow for more traditional material selections. Make sure to account for these conditions early in your planning stages, ensuring your choice of clamp will withstand whatever elements it might encounter while remaining functional over the duration of its use.
Materials and Their Importance
Cable clamps are typically made from materials like plastic, metal, or stainless steel. Each material has its own advantages, such as corrosion resistance or strength, which can affect the longevity and reliability of your installation. Plastic clamps tend to be lightweight and offer an affordable solution for light-duty applications, making them often preferable for indoor use where exposure to harsh conditions is minimal. Metals, including mild steel and galvanized variants, boast higher strength and stability, making them suitable for holding up larger cables in more demanding environments.
Stainless steel clamps come in when corrosion resistance is a priority. Given their innate ability to withstand rust and chemical exposure, these clamps are optimal for use in marine settings or heavy industrial areas. Some manufacturers also offer coated metal clamps that combine the best of both worlds—metal’s strength and a synthetic coating’s protection capabilities. When choosing materials, consider the installation location and the type of cables you’re securing. This can minimize maintenance and prolong the life span of both the clamps and the cables they manage.
In certain situations, the material choice goes beyond just durability concerns. Consider aspects such as weight limitations and color coding for organization. Lightweight plastic clamps can reduce overall setup weight—a crucial factor in automotive or aerospace applications. Likewise, colored plastic clamps help in distinguishing different cables, particularly in complex setups with extensive cable networks. Making these considerations enhances both functionality and aesthetics of your cable management design, ensuring it meets all practical and visual standards.
Size Matters: Matching Clamps to Cable Diameter
Ensuring that the clamp fits the cable snugly is crucial. A clamp that is too small can damage the cable, while one that is too large might not provide the necessary support. Always measure your cable diameter and choose a clamp that matches it correctly. This sizing not only affects the cable’s protection and the clamp’s holding strength—it also influences the ease of installation and future maintenance. Poor size matching could lead to frustrating complications down the line, undermining the efficacy of cable management.
Accurate size pairing ensures maximum efficiency in cable management. A well-fitted clamp will hold the cable securely and naturally in place even amid vibrations or movements, something crucial in environments such as automotive or marine industries where constant motion and shifting occur. Remember, the goal is to establish a firm but non-restrictive grip that safeguards the cable and its insulation. Inadequate fitting may contribute to abrasion or friction, which over time can shorten cable lifespan prompting frequent replacements and potential system downtimes.
Additionally, ensure you’re experimenting with multi-cable clamps if handling busier, more intricate setups. Multi-cable systems often demand unique components so each cable within the bundle receives adequate support and separation. Standard clamps, while suitable for singular connections, might either compress or inadequately separate multiple cables, leading to inefficiencies or complexities like signal interference. Always evaluate the entire system layout, identifying whether a multiple-channel or single-path clamp will benefit your design best, thus optimizing the functionality and organization of your cable network.
Tips for Installation and Maintenance
Proper installation is key to ensuring cable clamps perform effectively. While ease of installation can often depend on clamp type, having the right tools and understanding the steps involved can streamline the process. Begin by thoroughly planning your cable routing layout, identifying key attachment points, and spacing the clamps evenly to maintain a tidy and efficient line. The goal is to provide strong support without exerting excessive pressure that might lead to damage—whether that’s to the cable or its surroundings.
Regardless of how skillfully installed, regular maintenance for your cable clamps and the cables they secure is non-negotiable. Establish a routine inspection schedule to check for signs of wear and tear such as weakening grip, rust, or plastic degradation, which could compromise the reliability of cable support over time. Consider more frequent inspections in high-activity environments or areas subject to intense weathering or other external variables that could alter clamp performance. Proactively replacing weakened components prevents more extensive and costly repairs following a failure.
A simple trick to mitigate issues is lubrication—especially important for metal clamps operating in friction-inducing situations. Periodic applications of non-conductive grease can minimize mechanical wearing and extend operational efficacy. Additionally, verify that clamps remain tensioned as intended and haven’t shifted locations; misalignments can cause undesired friction, abrasion or stress on cables. Being proactive ensures your setup maintains its resilience, providing reliable cable support that aligns with project specifications while lengthening the life of the system significantly.
Final Thoughts on Choosing Cable Clamps
Selecting the right cable clamp might seem daunting at first, but by considering factors such as type, material, size, and environment, you can ensure your cables are securely managed. Remember, the right clamp not only enhances functionality but also prolongs the life of your cables, ultimately saving you time and resources in the long run.