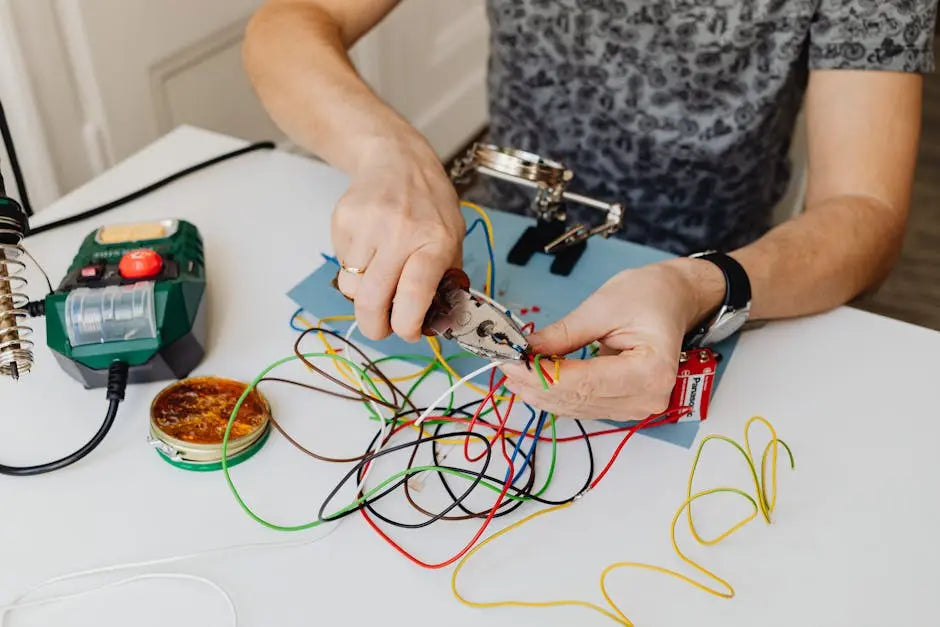
12 Common Mistakes to Avoid When Installing Butt Connectors
Share
Installing butt connectors may seem like a straightforward task, but even the most seasoned DIY enthusiasts can make slip-ups. In this guide, we will walk through the common pitfalls to avoid, ensuring a smooth and secure installation every time.
1. Skipping the Wire Strip
One of the most overlooked steps is properly stripping the wires before inserting them into the butt connector. Ensure each wire is stripped accurately to expose enough copper for a firm connection without damaging the strands. If the wires are stripped too much, you risk fraying or even breaking the strands, which could lead to weak connections or electrical faults. Stripping too little means the connection might not hold, leading to poor electrical transmission. Always use a wire stripper for precision and avoid using knives or scissors which can often lead to uneven stripping or damage.
Moreover, correctly stripping the wires ties into the broader topic of connection reliability. The exposed copper allows for optimal conduction, which is the bedrock of effective electrical connections. It’s also important to note that different projects may require different amounts of exposed wire, so always tailor your stripping accordingly. For more detailed guidelines on stripping wires, check resources provided by technical experts.
2. Choosing the Wrong Size Connector
Using the correct size connector for your wires is crucial. A mismatch can lead to a poor connection or could even damage the wires. Always check the gauge of your wires and select a connector that fits snugly. Many people overlook this step, assuming that close enough is good enough, but even slight differences can cause major issues such as electrical resistance or overheating. To ensure you have the right size, consult the manufacturer’s specifications or guidelines available online.
3. Neglecting a Proper Crimp
A secure crimp ensures a good electrical connection. A weak crimp can cause the connection to fail. Use a quality crimping tool and apply firm pressure to achieve a solid crimp. However, it’s crucial not to apply too much pressure, as this can damage the connector or the wire itself, leading to its failure. Techniques such as checking the crimp visually and conducting a light pull test can confirm the integrity of your crimp. It’s these small attention-to-detail steps that transform a good job into a great one.
4. Forgetting to Use Heat Shrink
Heat shrink tubing provides additional insulation and protection for your connection. Always remember to slide a piece of heat shrink over the wires before crimping, and apply heat after to seal the connection. Many forget this step in their haste to move on, leading to exposed connections that are susceptible to moisture and environmental damage. Using heat shrink not only adds a layer of protection but also makes the installation look professional and neat. To achieve optimal insulation, ensure that the heat shrink is the correct size and quality for your specific connectors.
5. Failing to Use the Right Tools
Using a general set of pliers instead of a designated crimping tool can result in a weak connection. Invest in the right tools for the job to ensure your connections are reliable. High-quality tools may cost more upfront, but they save time, prevent stress-related mistakes, and improve the quality of your work significantly. It’s worth consulting tool reviews or expert comparisons to choose the most effective equipment for your needs.
6. Overlooking Wire Alignment
Proper alignment of wires before crimping prevents incomplete connections and ensures electrical integrity. Make sure the wires are well aligned within the connector sleeve before applying a crimp. Misalignment can cause an uneven crimp, leading to a weak hold. Over time, vibrations or additional electrical load can cause these inadequate connections to fail, putting the entire system at risk.
7. Ignoring Weatherproofing
For outdoor or exposed connections, weatherproofing is essential. Protect connectors from moisture to prevent corrosion and failure, using waterproof heat shrink or silicone gel. Weatherproofing should be applied liberally to areas that are likely to encounter harsh conditions. Keep in mind that environmental protection not only involves a physical barrier but also considers factors like temperature changes and UV exposure, which can degrade materials over time.
8. Not Double-Checking the Connection
After installation, always test the connection with an appropriate device. This ensures the connection is holding firm and conducting power correctly. Skipping this step can lead to undetected issues. Redundancy in testing can catch errors before they become serious problems. Consider using multimeters to verify voltage and continuity, or even specialized testers if you’re working with complex systems.
9. Using Damaged Connectors
Inspect connectors for any damage or imperfections before use. A damaged connector can compromise the safety and effectiveness of your electrical installation. Some damages might not be visible at first glance, so when in doubt, don’t hesitate to use a magnifying glass or similar tool to inspect the integrity of the connectors. This proactive step can save time and money on future repairs and replacements.
10. Rushing Through the Process
Haste leads to mistakes that can be costly and time-consuming to rectify. Take your time to follow each step carefully, ensuring quality checks throughout the process. This doesn’t just pertain to installation but also proper planning and preparation. Gather all your necessary tools and materials beforehand to avoid last-minute scrambles that can lead to oversights. Furthermore, patience is key when waiting for solder to cool or heat shrink to set; rushing these stages can compromise joint stability.
11. Ignoring Wire Exposure Length
Ensure the length of exposed wire is neither too short nor too long. Too much exposure can leave connections vulnerable, whereas too little prevents a solid crimp. Carefully measure and adjust exposure lengths to meet the electrical standards of your specific project. Mismatched exposure lengths across multiple connections can decrease overall system efficiency, so standardized practices should be employed whenever possible.
12. Disregarding Connector Type
Different environments and wire types may require specific connectors. Choosing the correct type for your application, like insulated vs. non-insulated, is crucial for the safety and efficacy of your installation. Resistance to heat or moisture might be necessary depending on the connector’s intended environment, so always aim to match your connector type with the application’s unique requirements. Consulting with a specialist or using reference guides can be very useful in making the right selection.